The Rising Role of Plastic Injection Molders in Modern Manufacturing
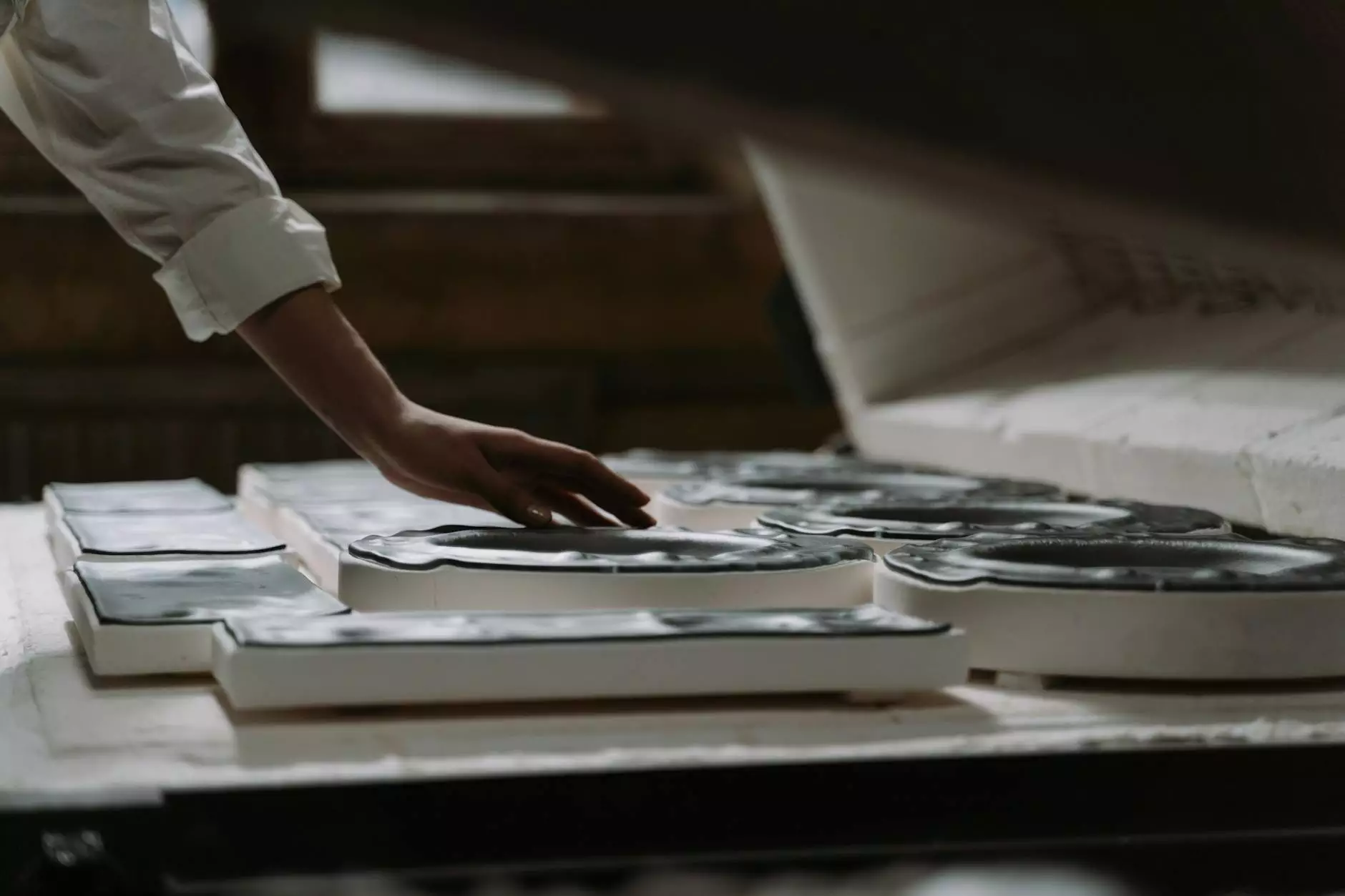
In today's fast-paced industrial landscape, the demand for efficiency, precision, and sustainability is greater than ever. One of the technologies that has significantly contributed to meeting these demands is plastic injection molding. In this article, we will delve into the world of plastic injection molders, examining their processes, benefits, applications, and the future scope of this pivotal manufacturing technique.
What is Plastic Injection Molding?
Plastic injection molding is a manufacturing process used for producing parts by injecting molten material into a mold. The process is widely utilized for creating a variety of products, allowing for high-speed production and remarkable flexibility in design. The steps involved in the process include:
- Material Selection: The type of plastic is chosen based on the required qualities of the final product.
- Heating: The selected plastic is heated until it becomes liquid.
- Injection: The molten plastic is injected into a mold cavity, where it takes shape.
- Cooling: The plastic is allowed to cool and solidify in the mold.
- Part Ejection: Once cooled, the mold opens, and the finished part is ejected.
Advantages of Using Plastic Injection Molders
The adoption of plastic injection molders in manufacturing comes with a plethora of advantages that help companies remain competitive. Here are some of the key benefits:
1. High Efficiency
Once a mold is created, the cycle time for producing each part can be very short, often just a few seconds per cycle. This leads to high volumes of production with minimal waste.
2. Design Flexibility
Injection molding allows for intricate designs and complex geometries, enabling manufacturers to create parts that would be impossible or expensive to produce using other methods.
3. Consistency and Precision
The automated nature of injection molding ensures that each part produced is consistent in size and shape, which is crucial for applications requiring precise tolerances.
4. Material Variety
A wide range of materials can be used in injection molding, including thermoplastics, thermosetting polymers, and even metals and ceramics when using specific molding techniques.
5. Cost-Effectiveness
Although the initial investment in molds can be high, the cost per part decreases significantly as production volume increases, making it a cost-effective solution for large-scale manufacturing.
Applications of Plastic Injection Molding
Plastic injection molders are employed across various industries, enabling innovations and advancements in product design and functionality. Some prominent applications include:
1. Automotive Industry
In the automotive sector, plastic injection molders are used to create a myriad of components, from interior panels to precise engine parts. The lightweight and durable plastics help improve fuel efficiency and performance.
2. Consumer Goods
From kitchenware to electronic housings, consumer goods leverage injection molding for aesthetic appeal and functional efficiency. The ability to customize colors and textures makes products more market-ready.
3. Medical Devices
The medical industry benefits greatly from injection molding, where precision and compliance with regulatory standards are paramount. Devices such as syringes, housings for diagnostic machines, and implantable devices are commonly produced using this technology.
4. Packaging Solutions
Plastic packaging solutions, including bottles, containers, and caps, are often created through injection molding, ensuring that products are not only durable but also visually appealing and functional.
5. Industrial Parts
Industrial components like gears, brackets, and fittings are crafted using injection molding to maintain consistency and reliability in functionality across various machines and equipment.
The Emerging Trends in Plastic Injection Molding
As the industry evolves, plastic injection molders are also adapting to new technologies and market demands. Here are some emerging trends reshaping the landscape:
1. Sustainability Initiatives
With a growing emphasis on environmental responsibility, many manufacturers are turning to sustainable materials and process improvements that reduce waste and energy consumption. Innovations such as biodegradable plastics are gaining popularity.
2. Smart Manufacturing
The integration of Internet of Things (IoT) technology enables real-time monitoring and optimization of the injection molding process. This leads to enhanced efficiency, predictive maintenance, and reduced downtime.
3. Advanced Materials
Research into new materials, such as reinforced plastics and composites, is expanding the potential applications of injection molding, allowing for stronger and lighter products.
4. Customization and Personalization
The demand for customizable products is on the rise, and injection molding technology is evolving to accommodate shorter production runs and personalized design requests from consumers.
Conclusion: The Future of Plastic Injection Molding
The future of plastic injection molders in manufacturing looks promising. With continuous advancements in technology, materials, and processes, they will play a pivotal role in meeting the ever-evolving demands of various industries. The ability to efficiently produce high-quality, customized products positions injection molding as not only a key player in manufacturing today but also as a driving force for economic growth, innovation, and sustainability for years to come.
For businesses looking to enhance their manufacturing capabilities, investing in plastic injection molding technologies can lead to significant returns. Whether in metal fabrication, consumer goods, or beyond, the advantages of utilizing this process cannot be overstated.